At the beginning of Chapter 5- Analysis of One way slabs, we saw a presentation which describes the basic details about the behaviour of Simply supported slabs. From the presentation, we get a clear understanding about the difference between a one way slab and a two way slab. When the distance ly increases, more and more load gets transferred in the other (x) direction, and the slab will become more like a one way slab. We have seen the limit beyond which we can design a slab supported on four sides as a one way slab: We take the ratio ly/lx. If this ratio is greater than 2, then we can design it as a one way slab even if it is supported on all the four sides. Here, it is important to note that ly is the longer span, and lx is the shorter span. This can be made clear based on the following fig.17.1:
Fig.17.1
Method of assigning lx and ly
Method of assigning lx and ly
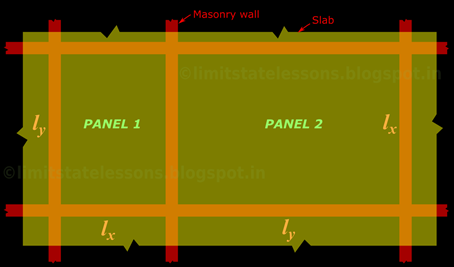
In the above fig., the part plan showing the slabs of a building is shown. For panel 1, the shorter span lx is horizontal and the longer span ly is vertical. But for panel 2, the shorter span lx is vertical and the longer span ly is horizontal. So we must not consider the conventional cartesian coordinate system while denoting the spans of a two way slab. Instead, we must follow the rule: Longer span is ly and shorter span is lx . Now we will see some more details about two way slabs:
In a one way slab, the slab is supported on two opposite walls. The loads will be transferred to these two walls only. But when the slab is supported on all the four sides, loads will be transferred to all the four walls. We can think of the total load acting on the slab, to be divided into two unequal shares. One share will be transferred in one direction, and the other share will be transferred in the perpendicular direction. If the slab is a perfect square, both the shares will be equal.
When a slab deflects into a cylindrical surface, there is curvature in one direction only. But when the slab deflects into a spherical surface, at any point on the surface, there is curvature in two mutually perpendicular directions. This means that all elements of the slab will experience a bending in two mutually perpendicular directions. So we must provide steel also in the two directions. The amount of steel that we have to provide in any one of these directions will depend on the bending moment in that direction. This bending moment in turn, will depend on the share of load in that direction. If the slab is a perfect square, then the bending moment in both the directions will be equal. So our next aim is to determine the share in each of the two mutually perpendicular directions.
Before we determine this, let us fix up the notations for the share in each direction, and also the bending moments in each direction. We have fixed up the notations for lx and ly based on the fig.17.1 Now we will consider fig.17.2 for loads and bending moments.
Fig.17.2
Notations for loads and bending moments
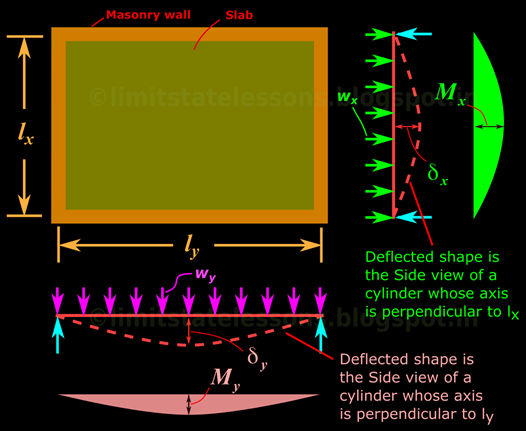
Notations for loads and bending moments
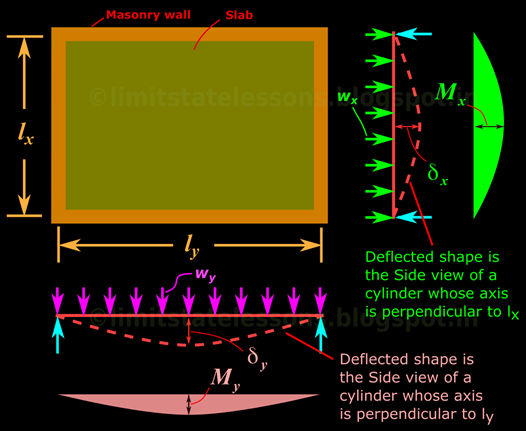
We can think about the bending of a two way slab in this way: The share which is transferred to the shorter walls bends the slab into a cylindrical shape. The share which is transferred to the longer walls also bends the slab into a similar cylindrical shape which is perpendicular to the first cylinder. The combined effect of these two cylindrical bends give the slab a spherical shape. Let us consider the two cylindrical bends separately as shown in the above fig.17.2. If wy was the only load present, and if the long walls were absent, then the slab will bend into a cylindrical shape, whose axis is perpendicular to ly. Similarly, If wx was the only load present, and if the short walls were absent, then the slab will bend into a cylindrical shape, whose axis is perpendicular to lx. Here wx and wy is the uniformly distributed loads over the whole area of the slab. As we will see in later sections, all portions of the slab will not experience the same uniform loads wx or wy. But for the ease of analysis, it is convenient to assume it as uniform, for a simply supported two way slab. Thus, from the two deflections shown separately, we can fix up the notations in an 'easy to remember' chart form:
● ly is the longer effective span, and lx is the shorter effective span
● The bending moment which makes the cylinder whose axis is perpendicular to ly is My, and the share which causes this Bending moment is wy .
● The bending moment which makes the cylinder whose axis is perpendicular to lx is Mx, and the share which causes this Bending moment is wx.
Now we can proceed to determine the quantity of these shares. Let us divide the slab into strips parallel to lx and ly as shown in the fig. below:
Fig.17.3
Dividing the slab into strips
Dividing the slab into strips
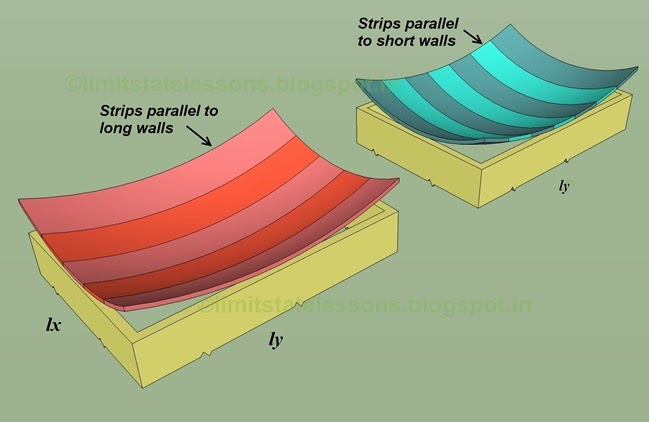
The red strips are parallel to ly and the blue strips are parallel to lx. The width of each of these strips is 1m. In the above fig., the strips are shown in two separate slabs. But actually, both the sets are to be considered in a single slab.
The chart that we prepared above, mentions about a cylinder whose axis is perpendicular to ly. It also mentions that the share that makes this cylinder is wy. Now, from the above fig.17.3, we can see that the cylinder whose axis is perpendicular to ly is made up of strips which are parallel to ly. So it follows that the share on each strip parallel to ly is wy. Similarly the share on each strip parallel to lx is wx. As mentioned earlier, wx and wy are not distributed uniformly over the whole area. So the load on strips also will not be uniform. Load on each strip will be different from the adjacent strip. We are assuming it to be uniform, for the ease of analysis. We can add these two points to the above chart and make it complete:
● ly is the longer effective span, and lx is the shorter effective span
● The bending moment which makes the cylinder whose axis is perpendicular to ly is My, and the share which causes this Bending moment is wy .
● The bending moment which makes the cylinder whose axis is perpendicular to lx is Mx, and the share which causes this Bending moment is wx.
● The share on each strip parallel to ly is wy
● The share on each strip parallel to lx is wx
For our discussion, we can take any one strip from each set as shown in the fig.17.4 below:
Fig.17.4
One strip from each set
One strip from each set
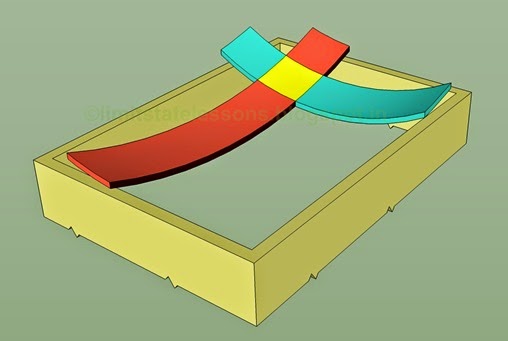
The intersection of the two strips is shown in yellow color. So the yellow portion belongs to both the strips. From the lessons in Strength of materials, we know how to calculate the deflection of a beam at any point. We can consider the red strip and blue strip in the fig., separately. First consider the red strip. If we know the distance to the yellow portion from any of the short walls, we can calculate the deflection of the beam at that portion. Similarly, considering the blue strip, if we know the distance to the yellow portion from any of the long walls, we can calculate the deflection of the blue strip at that portion. The deflection calculated by considering the two different strips should be the same. This is because, which ever strip we consider, the yellow portion has been displaced by the same amount.
The above calculation will be a lot more easier, if we consider the yellow portion to be at the intersection of two ‘central’ strips. This is shown in the fig.17.5 below:
In this case, the yellow portion is at the midpoint of each of the strips. The expression for deflection calculation at the midpoint of a beam is a simple one. In the next section we will write this expression for each of the two strips.
Copyright ©2015 limitstatelessons.blogspot.com - All Rights Reserved