Let us consider the red strip first. The red strip is the longer strip, parallel to ly, and having effective span ly. From 17.1 in the previous section, the share of load acting on it is wy. So the deflection of the yellow portion can be written as:

Similarly, the deflection of the yellow portion while considering the blue strip can be written as:

As the deflection of the yellow portion is same for both the strips, we can equate the above two as shown below:
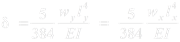
From this, we get a simple relation between wx and wy:
Eq.17.2:
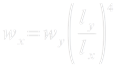
Based on the above relation, we can infer that wx will be always greater than wy, because the ratio ly/lx will always be greater than 1. We know that wx is the share that makes the cylinder whose axis is perpendicular to lx. So this is the load that gets transferred to the long walls. So we can say that the load transferred to the long walls is greater than the load transferred to the short walls.
If we add the two shares, we will get the total load w acting on the slab. That is:
Eq.17.3:
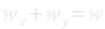
From Eqs.17.2 and 17.3 we will get
Eq.17.4:
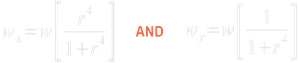
Where r = ly / lx
Steps leading to the derivation can be seen here
wx and wy are the UDL acting per one meter square area on the slab. The width of the strips that we are considering is 1m. So wx and wy will be the load acting per one meter length of the strips. When we know the load per meter length on the strip, we can calculate the maximum bending moment on that strip. Thus we can write:
Eq.17.5:
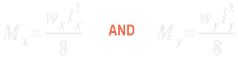
We must understand one more concept at this stage. wx and wy are loads per one square meter area, and they are the shares transferred in particular directions. So all the strips parallel to a particular direction will be experiencing the same load per one square meter area. That is., all the strips parallel to lx will be experiencing wx per unit area. And all the strips parallel to ly will be experiencing wy per unit area. So we can say that each of the strips parallel to lx will experience a maximum bending moment of wx lx2/8. And each of the strips parallel to ly will experience a maximum bending moment of wy ly2/8. So, the above Eq.17.5 which we derived based on a single strip is applicable to the whole slab.
Again, as mentioned before, in an actual two way slab, the load on each strip will be different from the adjacent strip. So the bending moment experienced by each strip will also be different from the adjacent strip. But we are assuming that all the strips in a particular set have the same load and bending moment. This assumption is for the ease of analysis. It will give conservative results for this type of a simply supported two way slab.
Now we will proceed to calculate the actual quantities in Eq.17.5. For this we must substitute for wx and wy from Eq.17.4. Thus we get:
Eq.17.6:

We can write the above equation in a form that is given in the code:
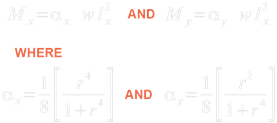
In the above Eq.17.7, we must take a special note of the expression for My. We can see that it is given in terms of lx, the smaller span. Also compare the expression for αy with that of My in Eq.17.6. The numerator has become r2 instead of 1.
We can make an important inference from Eq.17.7. The difference between Mx and My is αx and αy. The other quantities w and lx2 are the same. Now, αx has r4 in the numerator while αy has r2. The denominators are the same. As r will always be greater than 1, r4 will always be greater than r2. So αx will be greater than αy. Thus Mx will always be greater than My. So the steel required to resist Mx should be in the bottom most layer. This will give more effective depth, and thus greater Moment of resistance to the section. From 17.1, we know that Mx is acting parallel to lx. So we can write:
17.8:
The steel calculated from Mx is to be laid parallel to lx, and it should be in the bottom most layer.
The steel calculated from Mx is to be laid parallel to lx, and it should be in the bottom most layer.
Eq.17.7 is the final form given in cl.D-1.1 of the code. So we will follow it. The detailed steps leading to it’s derivation can be seen here.
The values of αx and αy are given in the table 27 of the code. A sample calculation can be done as follows:
Let r = ly/lx = 1.3. Then αx = r4 / 1 + r4 = 0.0926 and αy = r2 / 1+ r4 = 0.0548 The same values given in the table 27.
For using this table, first we must calculate r = ly/lx. then we take the value of αx and αy from the table. If r is an intermediate value, we can use linear interpolation. If we are using a computer, we can use Eq.17.7 directly. There is no need to obtain values from the table, and do the interpolation.
So each of the strip parallel to lx will experience a maximum bending moment of αxw lx2. And each of the strip parallel to ly will experience a maximum bending moment of αyw ly2 . Now the situation has become similar to a simple one way slab. In the case of a one way slab, we divide it into a number of strips. Then we find the maximum bending moment in any one strip, and the steel for resisting this BM is applicable to all the strips. The same happens in two way slab also. Only difference is that, we have to do the design two times, one for each direction. From the chart 17.1, Mx is bending the slab into a cylinder whose axis is perpendicular to lx. So we provide the steel required to resist Mx in a direction parallel to lx, as if to straighten the cylinder back to a plane surface. Similarly, we provide the steel required to resist My in a direction parallel to ly.
So now we have the equations for calculating the bending moments in a simply supported two way slab. But to use them, we need to find the load w. For this, we want to know the thickness of the slab to calculate the self wt. Also, we want the values of the effective spans lx and ly. In the next section we will see how these quantities are determined.
Copyright ©2015 limitstatelessons.blogspot.com - All Rights Reserved